UCD Physics with Astronomy & Space Science student Kevin Flanagan follows on from Rachel Dunwoody’s first post in a series covering their internship experience helping to build the I-LOFAR radio telescope in Birr.
This summer I’m fortunate enough to be part of the team which is helping to build the I-LOFAR (Irish-LOFAR) radio telescope in Birr, Offaly along with fellow UCD student Rachel Dunwoody. In Rachel’s first blog, she talked about how we laid the cables in the ground which will link the HBA and LBA antennae to the ILT container. I’m going to be talking about the next step in the operation, the construction of the HBA tiles. LOFAR is a large radio telescope located primarily in the Netherlands, but which has expanded to include stations in many countries across Europe, now including Ireland. The interesting thing about the construction of the I-LOFAR telescope is that it is largely carried out by students, under the supervision of Dr. Peter Gallagher and Dr. Joe McCauley from Trinity College, along with Hans and Zabet, two experienced supervisors who have each already helped to build 50 LOFAR stations!
I decided to apply for this internship largely due to the fact that it seemed so different to anything else I could have done this summer. It’s a very rare opportunity to be able to work on the construction of a large scale telescope such as this, which is in fact Ireland’s first since the famous Leviathan telescope was constructed on the same grounds of Birr Castle in the 1840s. I felt that it would help to give me a proper understanding of the work that goes into building such large scale telescopes. Telescopes like these are learnt about in class and the basics of their operation is theoretically understood, but chances to see their real inner workings and the practicalities of their operation and construction are few and far between.
The LOFAR telescope doesn’t look like what most people might imagine, it’s not a big radio dish like many radio telescopes of the past. It’s actually an array of antennae which each detect radio waves. There are two telescopes technically, one which works at higher frequencies (HBA) and another which works at lower frequencies (LBA). Combined the telescopes take up an area about the size of a football pitch.
The HBA was the first to be made. It consists of 96 tiles, each of which are constructed separately by teams of 3 to 6 people inside a large tent on the construction site. There are a number of steps to be carried out in creating the tiles, which are actually composed mainly of polystyrene, used due to its transparency to radio waves and low cost. It creates a structure for the antennae to stand in position and detect the radio waves without interference from the structure. A plastic container is first laid out, and a wire mesh, which is actually a mirror for radio waves, is placed inside, covering the bottom of the container. On top of this, a 4 x 4 grid is constructed with polystyrene. Each square of the grid is designed to hold a dipole antenna.
However before the antennae are placed inside, cables must be wound through the grid to connect each antenna to two summators (which basically collect all the information received by the tile).
Two cables are sourced from each square, due to the fact that each antenna receives two polarisations of radio signals, which basically means that they detect waves that oscillate along both the x and y axis. This means there are 32 cables winding through each tile. Winding the cables in such a fashion that the path they take is neither too long nor too short is an art in and of itself.
Once the cables are connected to the summators, the dipole antennae which we construct, which are triangular pieces of metal in a cylindrical polystyrene structure, are placed into each square. Receiver cards, which amplify the signal received by the antenna, are then placed in special slots in the polystyrene structure for each antenna and are connected to the antennae.
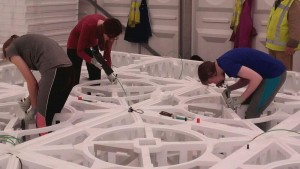
Megan(centre) connecting a receiver card to its cables, Rachel(right) inserting a receiver card into its slot and Julia(left) connecting a receiver card to a dipole antenna
After this the tile is tested by a computer programme to ensure that all components are in working order. The tile is then covered with some remarkably strong polystyrene lids, strong enough that several people can stand on them. They can supposedly hold over a thousand kilograms each! This doesn’t mean that all the polystyrene is indestructible however. It’s actually very easy to break other pieces with a trailing leg as you step into the tile, so care must be taken and spare pieces are definitely required.
Before we started building the tiles, our supervisor Hans told us that the record for the most number of HBA tiles created in one day was held by Poland, who made 8 tiles in one day in 2015. Naturally, we all wanted to beat this record, not so much for the sake of getting the telescope built more quickly, but really just to beat Poland. So that’s what we did, on two consecutive days! After many days of honing our tile building skills, one day we managed to build 10 and a half tiles, and the next day, after starting work an hour early at 8am, we built 11 tiles. The Usain Bolt of HBA tile building they call us (okay not really).
After we complete each tile, it’s loaded onto a platform which is carried to the field by a transporter. The summators are then connected to cables which we previously laid in the ground, which connect the tiles to the ILT container, where the data is collected and then sent to the main LOFAR hub in The Netherlands.
It’s amazing to see the HBA come together as the tiles build up on the field. It’s really fulfilling to be able to see all of our work lead to the completion of the telescope! In the next blog, Rachel will give an insight into the experience that we had during a typical day of the internship!